Appendix A - Inspection Panel Methodology
Selection of sites
The sites shall be selected using the AMPS database and in consultation with Transport Scotland to obtain a selection of sites laid across the whole Transport Scotland trunk road network that are coming up to their warranty period. In addition, further sites may be added at the discretion of Transport Scotland. Prior to the day of any visits, or during the visit if the site has not been visited before, the Convenor or Panel representative shall carry out a dynamic risk assessment for the sites to be visited and be responsible for making arrangements for the provision of any road closures and other precautions necessary to ensure that the inspections can be carried out in a safe and orderly manner. The route of the visit, methodology and risk assessment shall be sent electronically to all panel members in advance of the visits.
Inspection panel
The Inspection Panel shall consist of members agreed with Transport Scotland and, if appropriate, a local representative from either the Agent Authority and/or a representative from the client or Contracting/supplier side appropriate for the sites(s) to be inspected. The agreed members shall include a representative from WSP, who will act as Convenor. All members shall act in a personal capacity.
Members of Panel shall provide details of H&S training they have undergone related to working on or near a highway. Where necessary the Panel Members shall undertake an induction with the Regional Authority responsible for maintaining the highway on behalf of Transport Scotland. Panel members will require a letter of authority permitting access to motorways for inspection. Transport Scotland or their representative shall assess whether there are any deficiencies in the training that will inhibit the Member from being allowed on any or all of the sites and advise accordingly. In addition to the information provided in this document a separate H&S and Environmental Risk assessment is provided for all members of the Inspection team. All members are to confirm that both of these documents have been understood and that they are content with the Risks Assessments prior to commencing inspections.
Transport Scotland or their representative, after fixing the date for an inspection, shall inform other members as soon as possible before the inspection. A copy of this method of inspecting road trial sites shall be sent to any potential panel members who have not taken part before so that they can familiarise themselves with it.
No Panel Member shall take part in the inspection of a site if they have had an alcoholic drink that day.
Initial project briefing
Once the Inspection Panel has assembled, members shall be given an Inspection Panel Member's Report Forms. The itinerary of inspections and layout of each site will be provided in a separate document in advance to each of the panel members. The Convenor shall have an Inspection Panel Convenor's Report Form in addition to his/her Inspection Panel Member's Report Form.
If appropriate, the Convenor shall brief members on particular aims of the trial and any implications on the emphasis of that inspection. In particular, the Convenor shall supply a list of any project specific suffixes to be used and their interpretation.
The Panel shall agree on the weather conditions prevailing, and record it on their report forms. It is important to note both the weather (e.g. Sunny, Overcast, Raining) and surface condition (e.g. Wet, Drying, Dry) of the site.
The panel shall agree on the ‘stress’ level for each site and categorised as Low (L), Medium (M) or High (H). As an example, H will be commensurate with very heavy traffic flows, long uphill sections (with a high level of HGV traffic) and Junctions with high levels of turning traffic.
Site health and safety and risk assessment
The panel does not generally use closures for the inspections as these are of less than 15 minutes duration. However, if there is a closure in place on the site, not more than two vehicles shall be permitted to park in any closure, with personnel changing vehicles prior to entry when necessary. The preference is for as many people as practicable to be in each vehicle to minimise the number of vehicles in any closure. Inspection vehicles will be marked and equipped in accordance with Traffic Signs Manual, Chapter 8, Part 2: Operations, Section 05. When inspecting any site without a closure the site shall be inspected into the direction of oncoming traffic. Moving onto to the live carriageway shall not be permitted unless a spotter has been arranged whilst the member is in the live carriageway. Note: it is not permitted to go onto any live carriageway on motorways and high speed dual carriageways.
Where an inspection is to be undertaken from a hard shoulder of a motorway, without a closure, only two vehicles will be permitted, and they shall park with wheels facing the verge and no more than 100m apart. The inspection shall take place from the hard shoulder between the two vehicles. The panel shall inspect the site from the forward vehicle towards the rear vehicle (i.e. facing the traffic).
Motorway site inspections should take place when the traffic flows are at reduced levels. These surveys should therefore be planned to take place outside peak hour traffic. Should the traffic flows be considered very high at the time of arrival on site the inspection should be deferred.
Where parking availability is not known prior to arrival on site a suitable location off carriageway shall be sought so that access/egress from vehicles is safe and the vehicles do not inhibit the safety of other motorists or pedestrians.
When sites have been visited previously, the previous risk assessment may be used but should be reassessed in case circumstances have changed. When visiting sites for the first time, the general risk assessment can be used, but any specific points noted and kept for future reference. Any amendment to specific risk assessments shall be recorded.
All panel members shall confirm their agreement and register their understanding of the risk assessment and H&S requirements.
Personal protection equipment
All Panel Members shall wear a high visibility long-sleeved vest or coat and trousers to BS EN 471, Table 1: Class 3 or better. Note: the coat/vest shall be done up during all inspections.
All Panel Members shall also wear safety footwear and compliant with the requirements of the Network managements of the region being inspected.
All panel members shall wear a hard hat during inspections.
Any Panel Member not properly attired shall be asked to leave the site until the situation is rectified to the satisfaction of the Client / Convenor.
Inspection
The Panel shall walk each section in turn, studying the condition as closely as practicable. Where possible, Members shall stop and look back at intervals along each section so as to view the surfacing with the light in a different direction.
As far as practicable, Panel Members shall stay together as a group when inspecting and not get extended which could be distracting to road users. The Panel shall walk, in order of preference if available:
- behind any barrier in close proximity to the section of road being inspected;
- on a footpath alongside the section of the road being inspected;
- with a lay-by alongside the section of the road being inspected;
- on the verge alongside the section of the road being inspected; or
- along the road being inspected.
Panel Members shall walk towards the oncoming traffic wherever practicable.
Localised areas that have been subject to untypical mechanical or chemical actions (e.g. damage caused by a vehicle running on its wheel-rim or by a diesel spillage) shall be ignored. If variations are on a larger scale, such as between wagon loads when laid, the section shall be assessed in sub-sections. WSP shall try to establish the reasons for any large differences by checking the laying records and the compositional analysis at the appropriate time.
Members shall record on their Inspection Panel Member's Report Form a mark for each section soon after inspecting it. Whilst members can discuss points of interest noted along the section, they shall not reveal how they intend to mark that section until all members have recorded their individual mark.
Marks will generally be collected by the convener after each site has been inspected. Where the inspections are from the hard shoulder of the motorway the marks will be collected after moving off site to minimise the time on the hard shoulder.
Marking
Each section shall be assessed on the basis of its current serviceability irrespective of the elapsed time since it was laid. A detailed marking table is provided for reference on site, Table A-1. In considering the serviceability of the surfacing, the aspects in Table A-1 for the specific type of surfacing shall be considered, together with any project related aspects given in the initial briefing. If any of the aspects are evident to a significant degree on the section, the relevant suffix from Table A-1 shall be applied to the basic marking. Suffix v shall not be applied to a section marked as t, nor + to one marked –.
Joints are a particular issue with respect to initiation of fretting and subsequent failure of the surfacing so additional suffices have been added to record the presence of open joints and joints where fretting and ravelling have occurred. Note: an open joint (jo) refers to joints that are clearly susceptible to the ingress of water and have been inadequately sealed at the time of construction
A second overall assessment table is also proved for reference on site, Table A-2. Once any appropriate fault suffixes have been assigned, the basic mark shall be allocated from the 7-point scale in Table A-2. Intermediate markings between scales shall not be given. When considering the markings, any sections that warrant a suffix cannot have a basic mark of G or better (one exception is G jo where the mat itself is considered to be in a good condition but the joint considered open (see above).

Table A-1 The marking suffixes table, giving details of classification of surface failure type, which is referred to on site when assessing road surfaces.
Overall assessment
When each member has reported his individual result, the Convenor shall convert them using the transformation:
E = 6; G = 5; M = 4; A = 3; S = 2; P = 1; and B = 0.
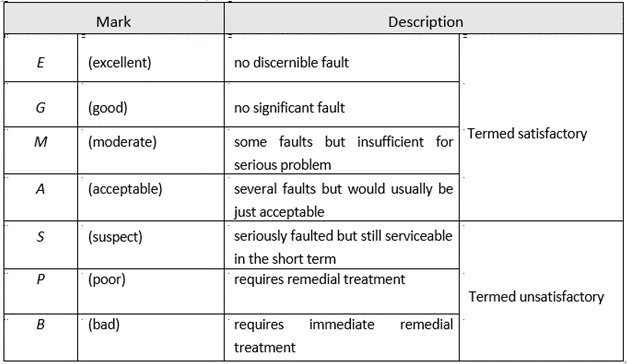
Table A-2 The main marking table referred to on site, giving descriptors of general road surface condition.
The mean of the individual results shall be calculated to one decimal place and converted back into the Panel marking, rounding off as follows:
- .8 to .2 - Basic marking with symbol/s; and
- .3 to .7 - Intermediate marking with symbol/s.
Suffixes shall be applied to the Panel marking when at least a third of the Panel members, rounded up, give it on their individual markings provided:
- the basic Panel marking is not G or better, as then no suffixes can be applied (with the exception of jo); and
- both v and t, or both + and –, are given, when only one of each pair can be applied to the basic Panel marking. The choice shall be based on the number of times the different suffixes occur on individual markings (in the case of a tie, the Convenor shall decide).
The number of panel members shall be noted when reporting the results.
Confidentiality
Whilst the Panel marking can be reported, the individual marks allocated by members of the Panel shall be treated in confidence. This limitation is to allow members to make judgements as to the condition of the trial sections without consideration of the commercial interests of their organisation.